From Toilet Paper to Transformers: Standards Keeps the PUD Safe – and Efficient
< All Stories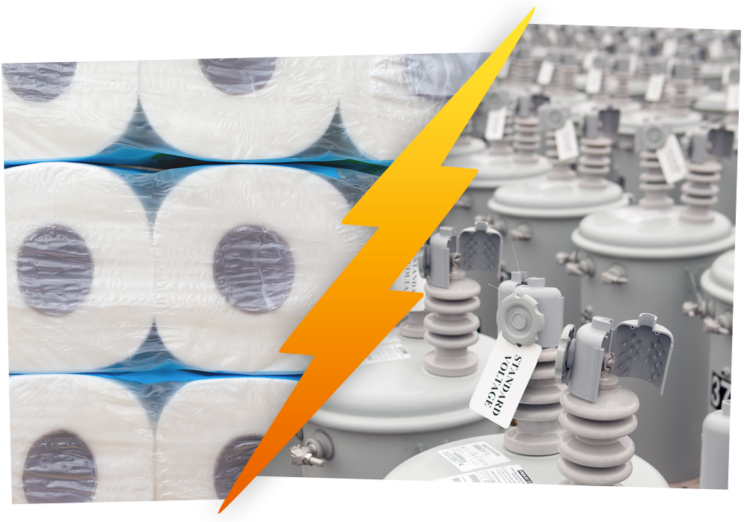
When we need assistance analyzing a product – any product – the PUD’s Standards team is who we go to for help.
The group studies and scrutinizes to find the best possible solutions when it comes to the utility’s needs. For everything from decals, fuel, tools, to yes, even toilet paper, the group makes sure products meet the PUD’s highest … um… standards.
“We’re the stewards of the materials,” said Tyler, a Principal Engineer in the PUD’s Standards department. “That’s from toilet paper up to transformers. It’s equipment, chemicals, paint, fuel, things that we use all over. We touch almost every corner of the PUD. We’re kind of a catch all for a lot of stuff.”
Several factors go into every recommendation. The goal is to provide the best value. Because we are a public agency, the PUD is required to do the lowest cost that meets the specification.
There are other factors the Standards team takes into consideration too. The group works with Environmental Affairs to see if there are any environmental concerns, or if it will cost anything to dispose of a product once we are done using it. They also factor in supply-chain constraints and warranties.
But one consideration is far and away the most important: safety.
“That’s consideration No. 1. To the point that we don’t even think about it anymore,” Tyler said. “If an item has any symptoms of not being safe, we will figure that out very quickly. Manufacturers will tell us, ‘Oh, no one says anything about that.’ Well, we will.”
While day-to-day requests are things you might expect, some unique items do come across the team’s desk. In the past, Tyler has helped look at wheel chocks for vehicles. Soap dispensers have been analyzed. Standards has looked at which dog biscuits were the best to carry for our furry friends and found the best Mylar balloons for ARC Trailer demonstrations to guarantee an arc.
Another recent project was figuring out what electrolytes to get stocked in our Warehouse. They got a bunch of feedback and analyzed options for sugar content, flavor and method of consumption (like an individual serving packet vs. a large jug with pre-made beverage).
“It slowly gets narrowed down going through committees and feedback,” Tyler said. “With electrolytes, it became, ‘We want these products, and we would prefer they don’t have a ton of sugar.’ Then it’s just getting everyone to agree on flavors. That’s when we hit the challenge.”
Sometimes the group can’t find exactly what they’re looking for. That’s when they get to work helping invent new things from scratch. The group recently worked with Everett Engineering to create a lifting device for ductile iron poles for crews to help pick them up more safely.
“We made a list of requirements, and they built a prototype,” Tyler said. “It’s cool getting to help create a product that solves a problem that there is currently no solution for. That’s a big part of our job: to be problem solvers.”
Most challenges involve a fair amount of collaboration with other groups around the PUD, especially Line Construction. The Standards team is always working to ensure that whatever the PUD acquires is exactly what the requestor is looking for.
“Things are very different on paper than they are in practical application,” Tyler said. “It could look great sitting in an office chair, but then you get it in the field – like in the training yard – and it becomes obvious that what sounded good isn’t going to be practical in the end.”